Комплексні рішення організації виробництв
Про компанію
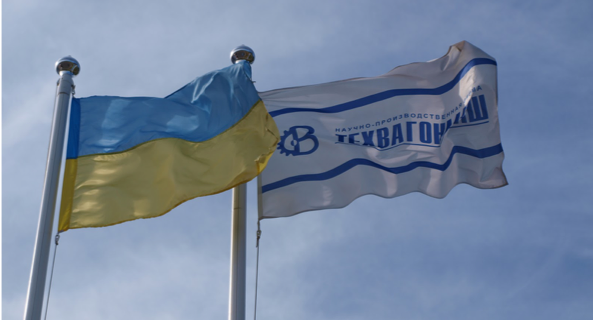
Науково-виробнича фірма «Техвагонмаш» – один із провідних розробників та виробників спеціального технологічного обладнання для підприємств транспортного машинобудування. Компанія заснована у…
Новини компанії НВФ “Техвагонмаш
доступні по посиланню
Підписатися на
розсилку
Підписатися на розсилку
Натискаючи на кнопку, ви даєте
згоду на обробку персональних
даних та отримання нашої новинної розсилки